A process can make or break your business. On the one hand, the right process can help you reduce costs, increase revenue and productivity, and provide a better experience to customers. On the other hand, a poorly designed process can drive your employees crazy, make customers unhappy, and cost you money. For example, research suggests the healthcare industry lost $16.3 billion in 2020 due to inefficient processes. Process optimization can help you identify non-efficient processes in your business and find improvement opportunities with speed. In this article, we’ll introduce you to the basics of process optimization so that you can start on your right foot.
Let’s start with a simple question.
What is Business Process Optimization?
To better explain this concept, we must first explain what a process is. In short, a process is a collection of related tasks or activities that, together, create a specific output. For instance, some of the tasks involved in a typical sales process might be:
- Sales rep meets a new prospect and logs a new opportunity in the CRM system
- Sales rep schedules a meeting with the prospect
- Sales rep meets with prospect, presents a sales deck, and conducts a demo
- Prospect indicates they want to sign-up
- Sales rep updates the opportunity record in the CRM system to a status of Closed/Won
By following this sequence of steps (input), you get a new deal (output). Now, process optimization is focused on designing, measuring, and improving a given process. It seeks to maximize outcomes while minimizing the resources used in the system.
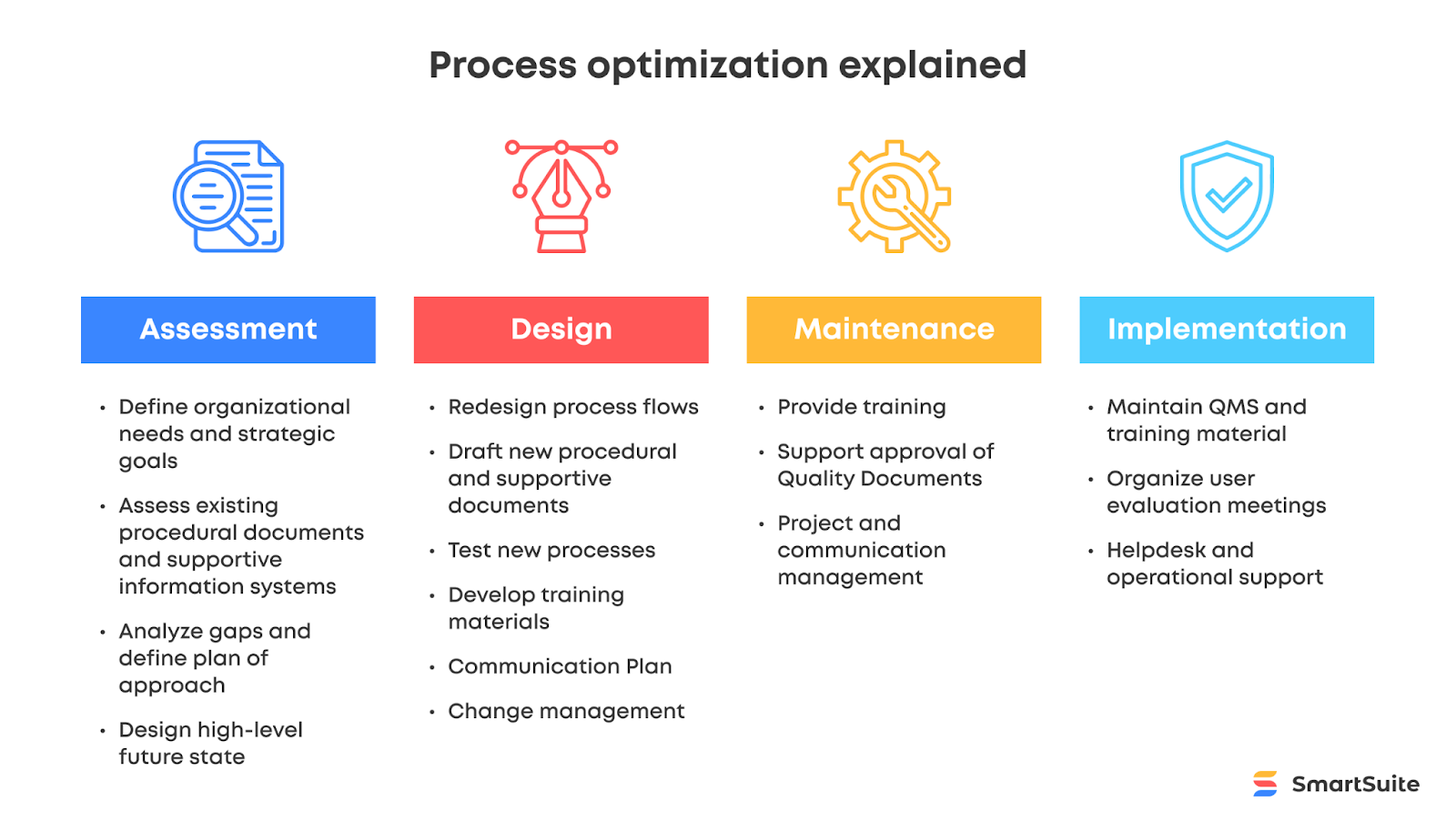
Process optimization finds out which process activities aren’t necessary or could be combined to create efficiencies. Getting back to the website example, you might figure out that WordPress is no longer the most efficient technology for building websites. To improve your process, you could replace that step and use a more effective technology.
Popular Process Optimization Methodologies
Now that you understand what process optimization is, let’s explore some of the popular methodologies to implement it in your business.
Total Quality Management (TQM)
TQM is a process that focuses on improving quality within an organization. This leads to increased customer satisfaction and a reduction in costs. Edward Deming, an American engineer, is "credited" with inventing TQM. He's also known for his series of 14 management principles. The focus of Deming’s work was "prevention" rather than merely trying to fix problems after they arise.
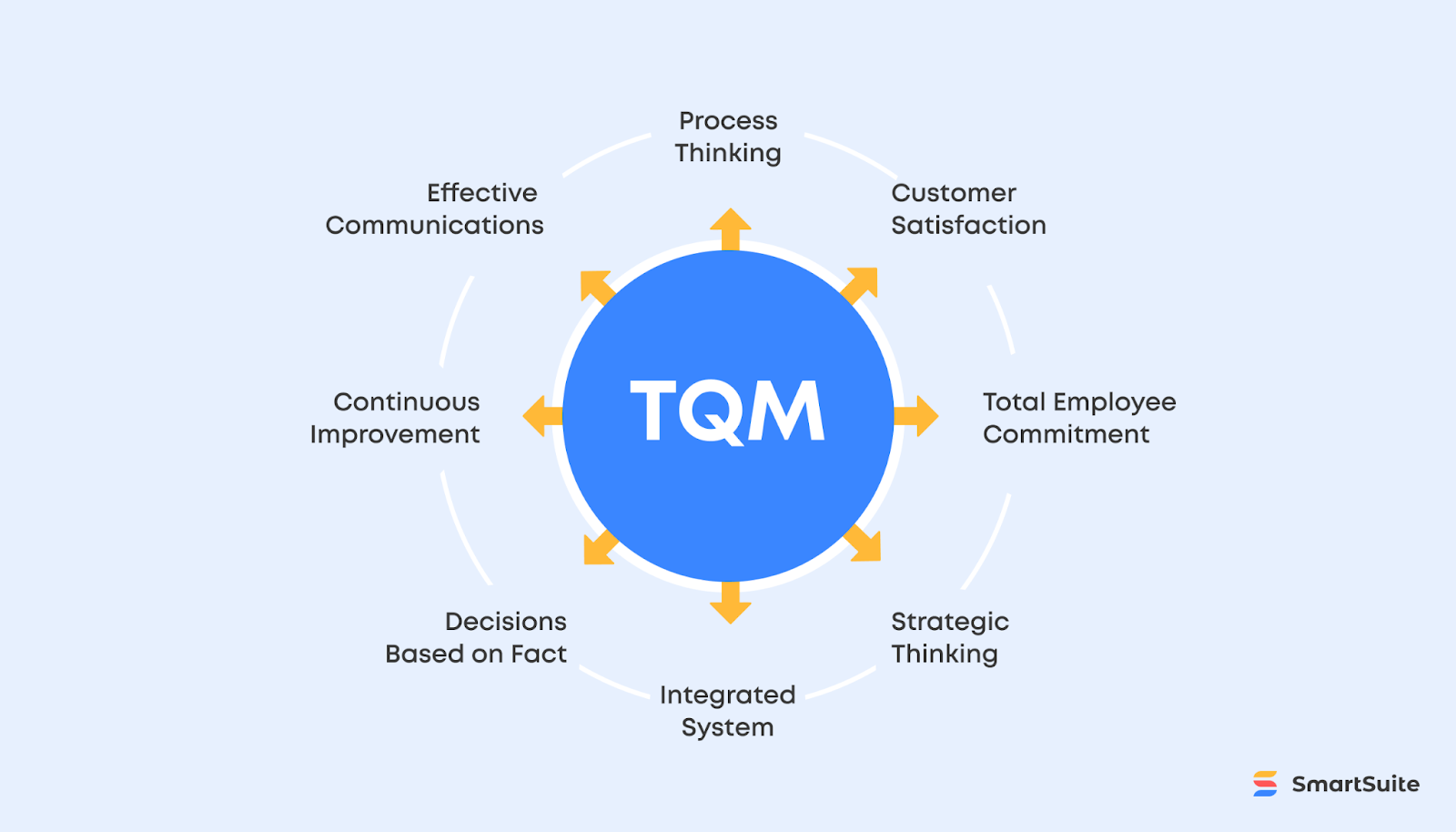
In a nutshell, here's how TQM works:
- Create a customer-centric culture
- Involve employees, suppliers, and customers in product design, planning, and problem-solving
- Continuously improve process performance
TQM focuses on improving all processes within an organization, not just manufacturing (which is where most organizations focus their efforts).
Agile Management
The Agile process optimization methodology focuses on speed, simplicity, and customer satisfaction by doing just enough work to meet customers’ needs. The Agile Manifesto states that teams should value customer collaboration over contract negotiation while emphasizing adaptability. At the core of this methodology are the values of “individuals and interactions over processes and tools,” “working software over comprehensive documentation,” and “customer collaboration over contract negotiation.”
How can we use Agile?
The Agile methodology can be used in process optimization to build a minimum viable product, release small parts of it frequently, and then gather feedback from the client. This incremental development model isn’t suitable for processes that need long-term planning (such as financial or HR processes), but it can be extremely useful in a dynamic environment.
Lean Six Sigma
Lean Six Sigma is a quality management method that focuses on defect prevention rather than defect detection. This creates a shift in focus from solving problems with quick answers (firefighting) to eliminating the root cause of the problem in a more efficient way with quick solutions.
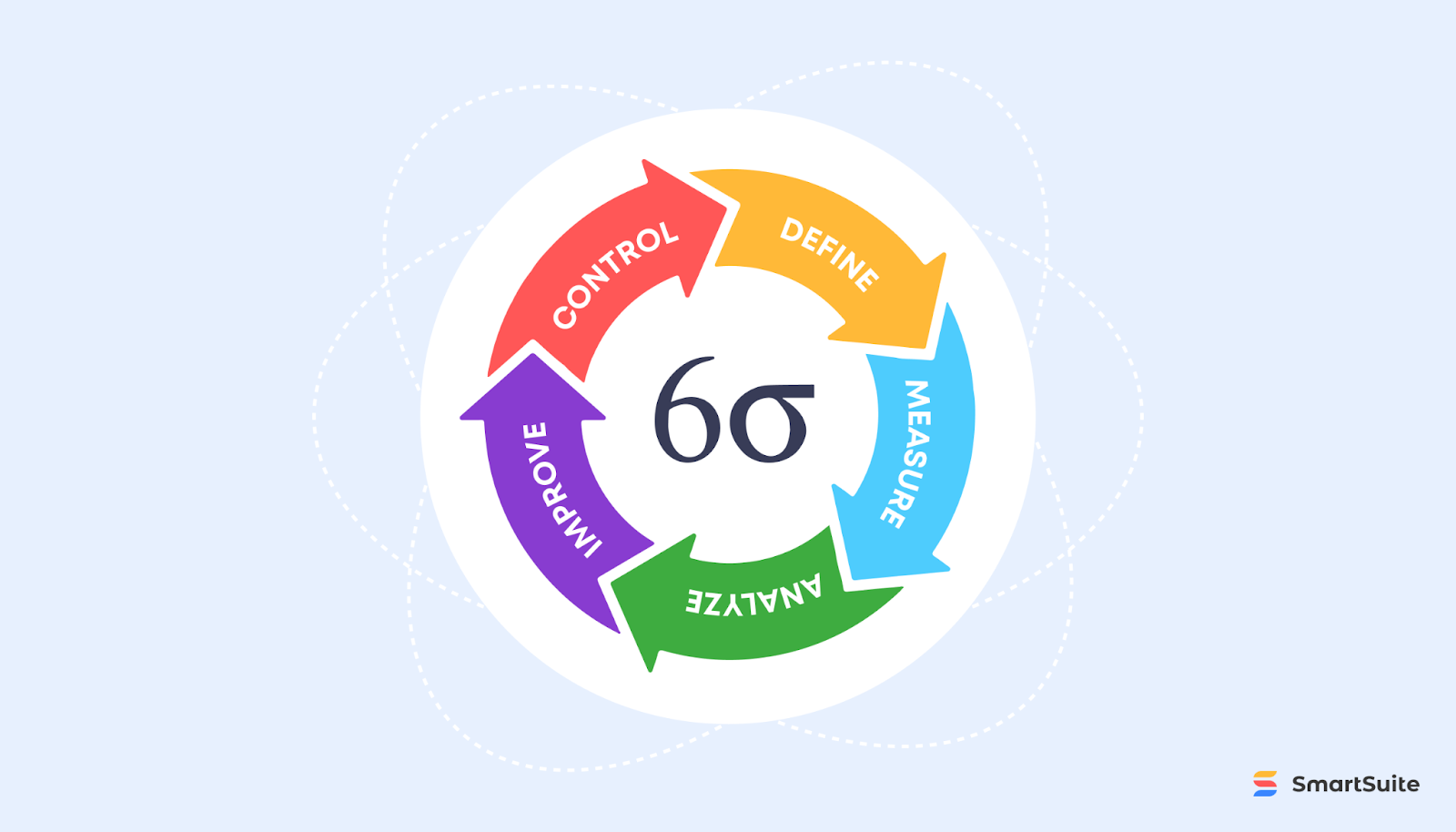
One of the main process optimization tools in Lean Six Sigma is the DMAIC model. DMAIC stands for Define, Measure, Analyze, Improve, and Control. Even though DMAIC is an integral element of Lean Six Sigma, it can be implemented as a standalone model. In the next section, we’ll explore this model in-depth.
How Can You Actually Optimize a Process?
As we stated earlier, there are different methodologies you can use to optimize a process. For the sake of brevity, though, we’ll focus on DMAIC. DMAIC is a great business process optimization model that can be applied to almost any industry, and it’s easy to implement.
Let’s break down the actual steps:
1. Define Process Capabilities
Process improvement starts with process definition. This is where the team analyzes current process capabilities and works out a checklist of targets. This step also involves setting goals, clarifying your understanding of the problem, and writing down any assumptions you might have. The process has to be mapped and described in detail. You should define process boundaries, process goals, and metrics to measure. This will help you identify problems in later stages.
2. Measure Process Performance
In this phase, you define what key performance indicators you want to improve and also measure your current performance against your goals. You also need to carefully investigate how your process is currently operating. Before you begin to make changes to your process, you need to know where you currently stand.
First, you should measure your process in terms of speed and efficiency. Then, you should measure your process in terms of process costs. You can also check process quality. The point is that all process data should be based on the metrics that you define. You can use both quantitative and qualitative methods to gather performance data.
3. Analyze Process to Find Sources of Variation
Any process goes through three phases:
- Setup phase: Process is set up, and initial conditions are established.
- Steady phase: Period in which variables are held constant.
- Teardown phase: Process variables return to their initial conditions after the process has been completed.
During the steady period of any process, there’s little to no variation in process data. Variation only exists during setup and teardown. By focusing on process performance during steady state periods, process optimization teams can minimize variation and establish process stability. Put simply, your team should use the data from the previous step to identify possible sources of variation in performance. You should also look for the root cause of problems and potential improvement opportunities in your processes.
4. Improve Process Based on Findings From Previous Steps
In this phase, you use the findings from the previous phase to create potential solutions to your problems. You then need to test these ideas, pick the best one, and fully implement it. For example, you might find that an unbalanced process can lead to lower quality. In this case, you could implement frequent inspections and testing or better supervision to solve the problem. Or you might discover that a lack of staff in some areas leads to longer waiting times. A potential solution could be to hire more employees, redistribute your current team, or change the work times. The point is that your team should use their process knowledge to implement new strategies that improve your current performance.
5. Control Process to Ensure Sustained Improvement
In this final phase, you need to make sure your improvements don’t wear off and revert back to their original state. This step is where the new process becomes part of your standard operating procedure (SOP). How long will it take you to reach this point? Well, that depends on the size and complexity of the process. Your process optimization project could take more than six months, or only last a few weeks. At the end of the day, this is an iterative process. Every optimization must undergo a series of tests before it can become part of the standard process. You’ll need to run multiple process validation tests to ensure the process is sustainable.
Why Process Optimization Software is Essential
Process optimization can be complex, as it involves many variables. You need to oversee the performance of multiple metrics at the same time and make sure there’s a balance between stability and efficiency. Doing this manually is virtually impossible. Here’s where process optimization software comes into play. By tapping into the right software, you can save time and resources and improve your optimization efforts. IT leaders say that software helps employees complete tasks 10–50% faster. That’s one of the reasons 50% of business executives say they’ll speed up the adoption of software to automate repetitive work. With that said, the question becomes, how can you choose the right platform for your organization?
Let’s explore a few essential features to look for:
Visual Interface
Here’s the truth: You can’t improve a process if you can't see it.
That’s why before choosing a specific platform, you should make sure it offers a visual and interactive user interface. This way, you can map out your processes more easily and point out issues and improvements as they arise. With SmartSuite, for example, everything is visual and interactive from the beginning.
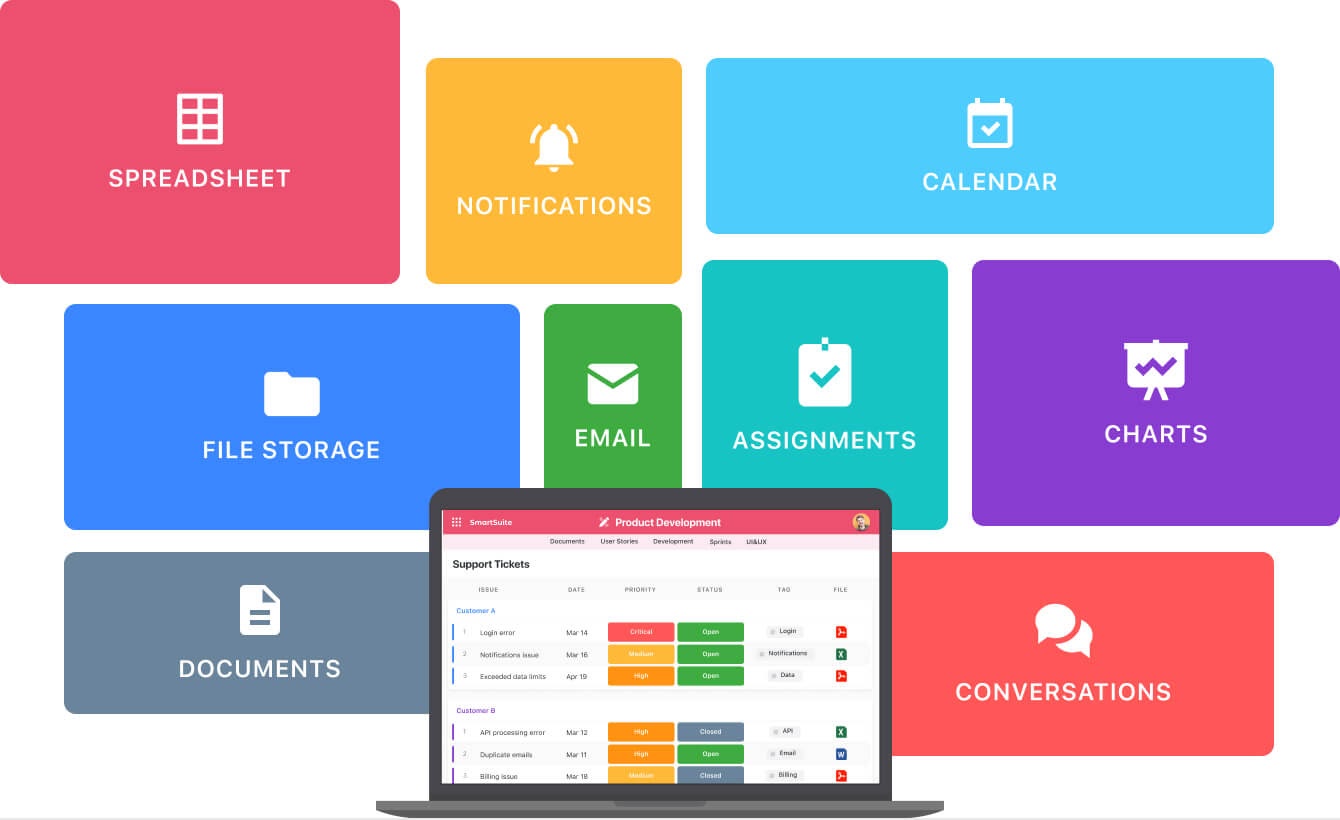
You get access to multiple building blocks that you can move around at will to design a platform that fits your exact needs. You can also use these “blocks” to streamline any type of workflow in just a couple of clicks.
SmartSuite also provides you with predesigned templates for processes across multiple industries. These templates are fully customizable, and you can adapt them to your processes fast. For instance, let's say that you want to optimize your product development process. In this case, you could simply install our product management template, invite your team to the platform, and adapt the template to your needs.
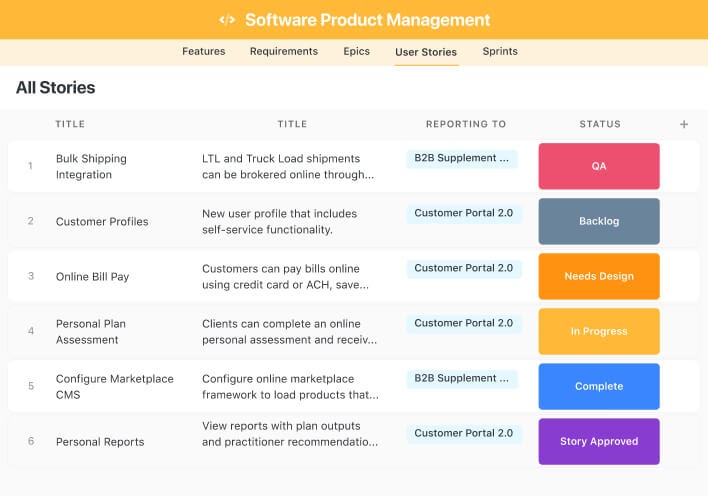
It’s that simple. This way, you can jump-start your process optimization initiatives and get started much faster.
Advanced Search
Search capabilities are key to process optimization. All your data points need to be searchable and easily filterable by anyone who needs to address them. That’s why every process optimization software worth its salt must provide you with an advanced search feature. With SmartSuite, you can easily search for your process data by time frame, type of issue, and category.
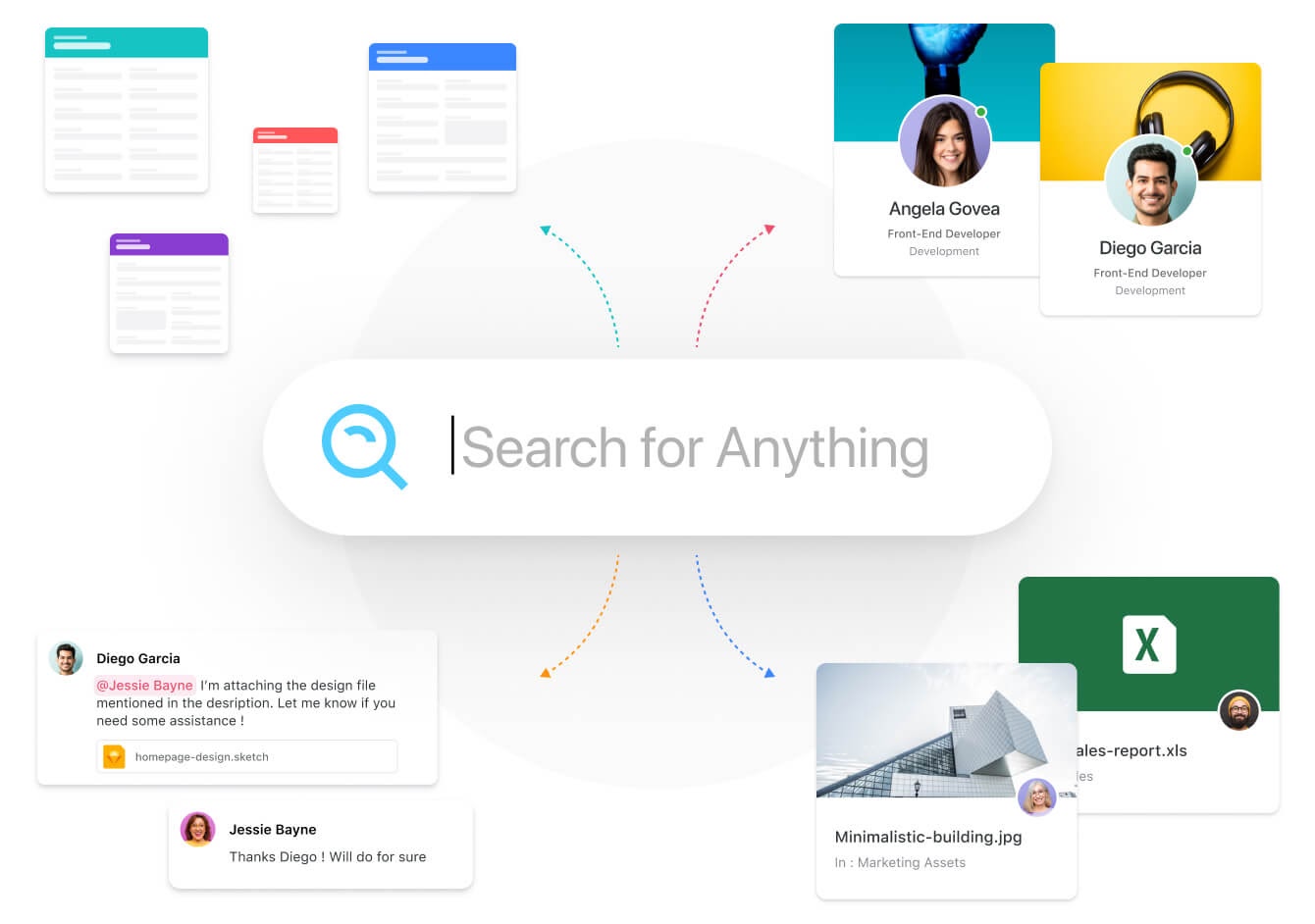
This way, you can filter out all the data points that aren’t relevant to the root cause you’re investigating and only work with those that are.
Collaboration Features
Process optimization is a collaborative effort. Make sure your chosen process optimization software allows for multiple users, collaboration, and sharing of all required documents. This is especially crucial for remote and hybrid teams that require constant communication. Collaborative software helps teams work more efficiently, ensuring that everyone has access to accurate information at their fingertips.
With SmartSuite, for example, you can share files, update status in real-time, conduct point-to-point messaging, have file version control, and even access the same document from simultaneous connections.
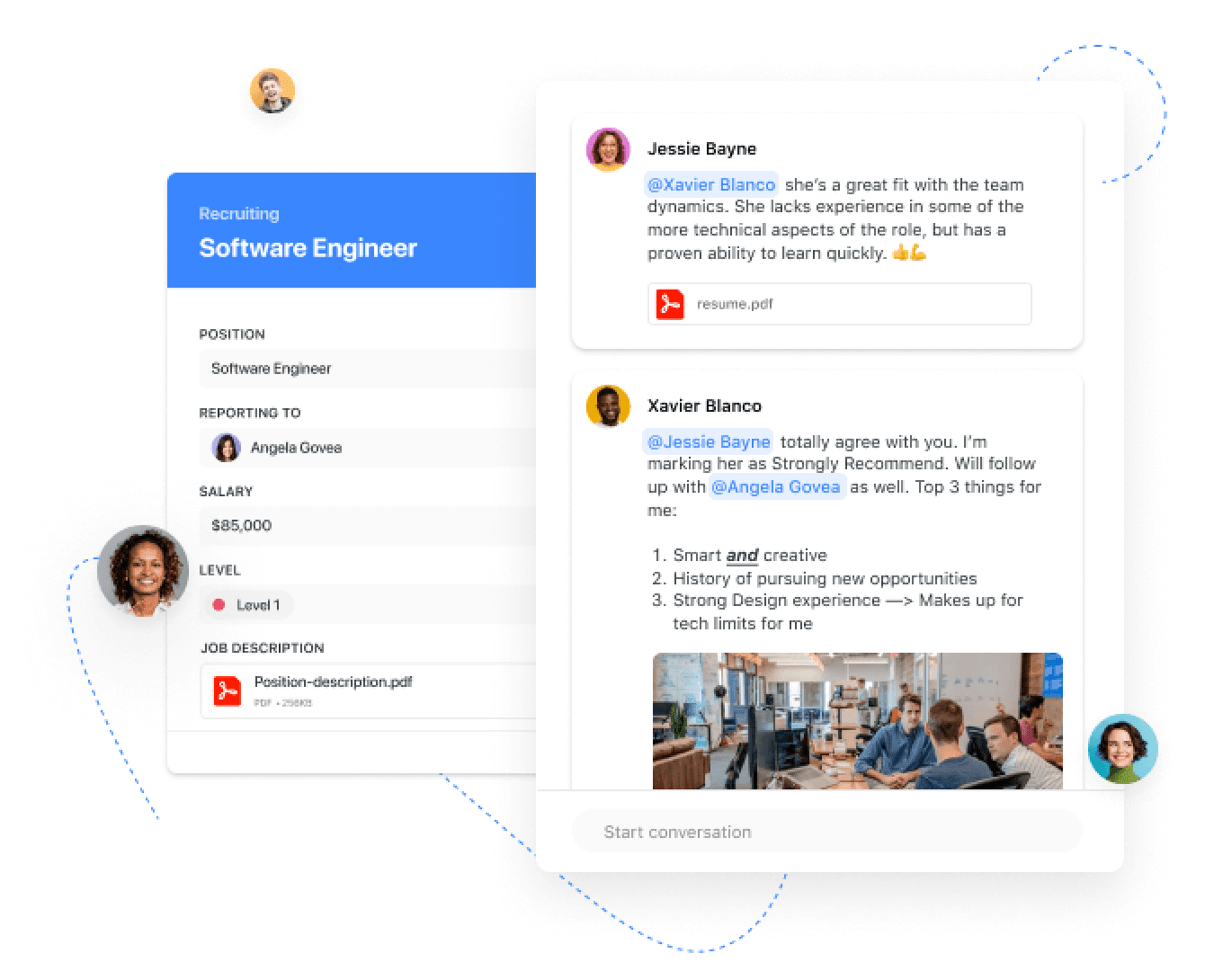
You can also track every action taken on a document, review comments, and see who’s working on what.
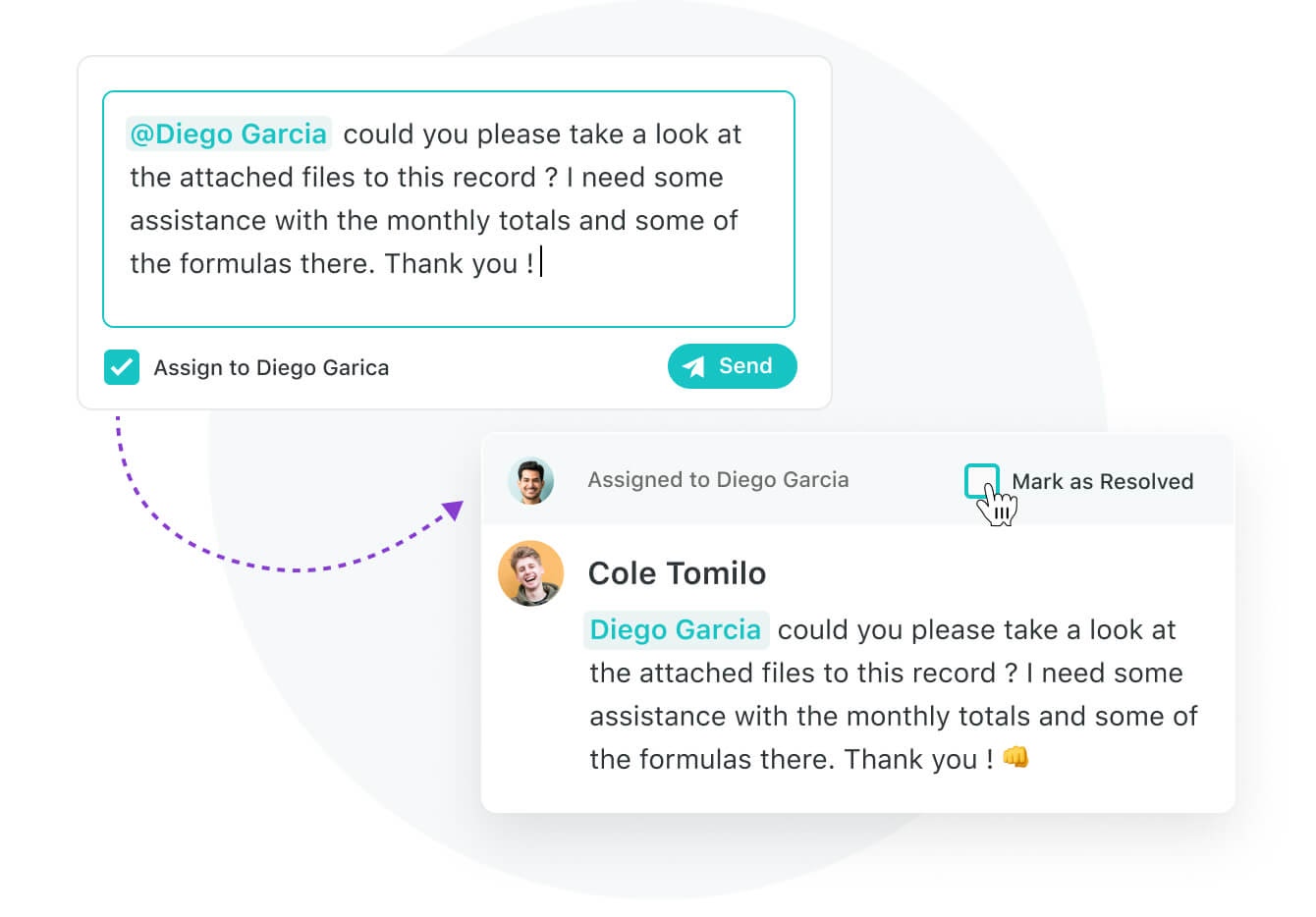
This way, you can have more control over all your process information.
Automations
Did you know that 1/3 of the tasks in 60% of all occupations can be automated? Plus, more than 50% of business owners agree that process automation inevitably reduces human error. If your chosen platform doesn’t offer workflow automation, you’re leaving a huge opportunity for improvement on the table. With process optimization software, process automation isn’t just possible but also extremely easy to implement.
For example, with SmartSuite, you can create automation rules to streamline any type of task or activity, including:
- Repetitive tasks
- Item creation
- Notifications and tagging
- Task dependencies
- Deadlines
- Status changes
And many more.
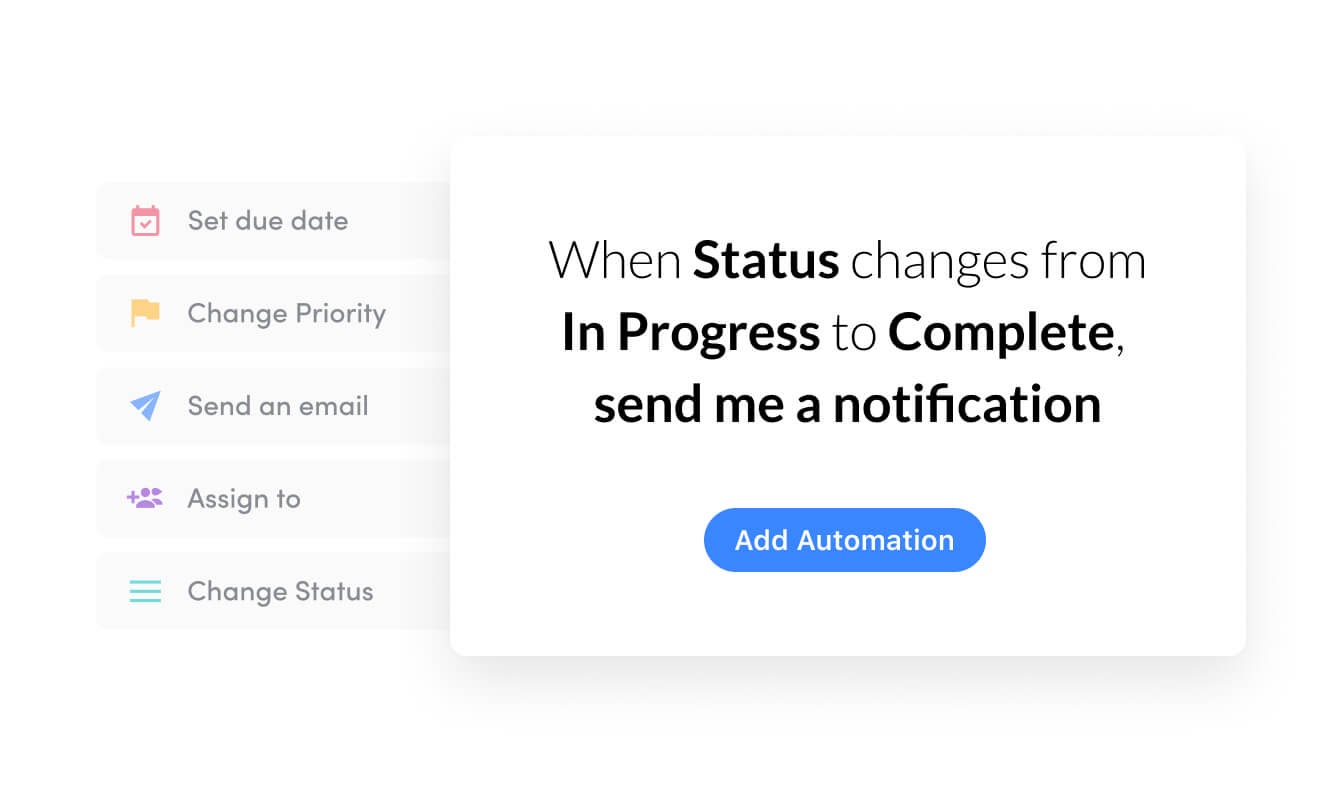
You can also schedule process redesigns, automate actions, and monitor performance with ease.
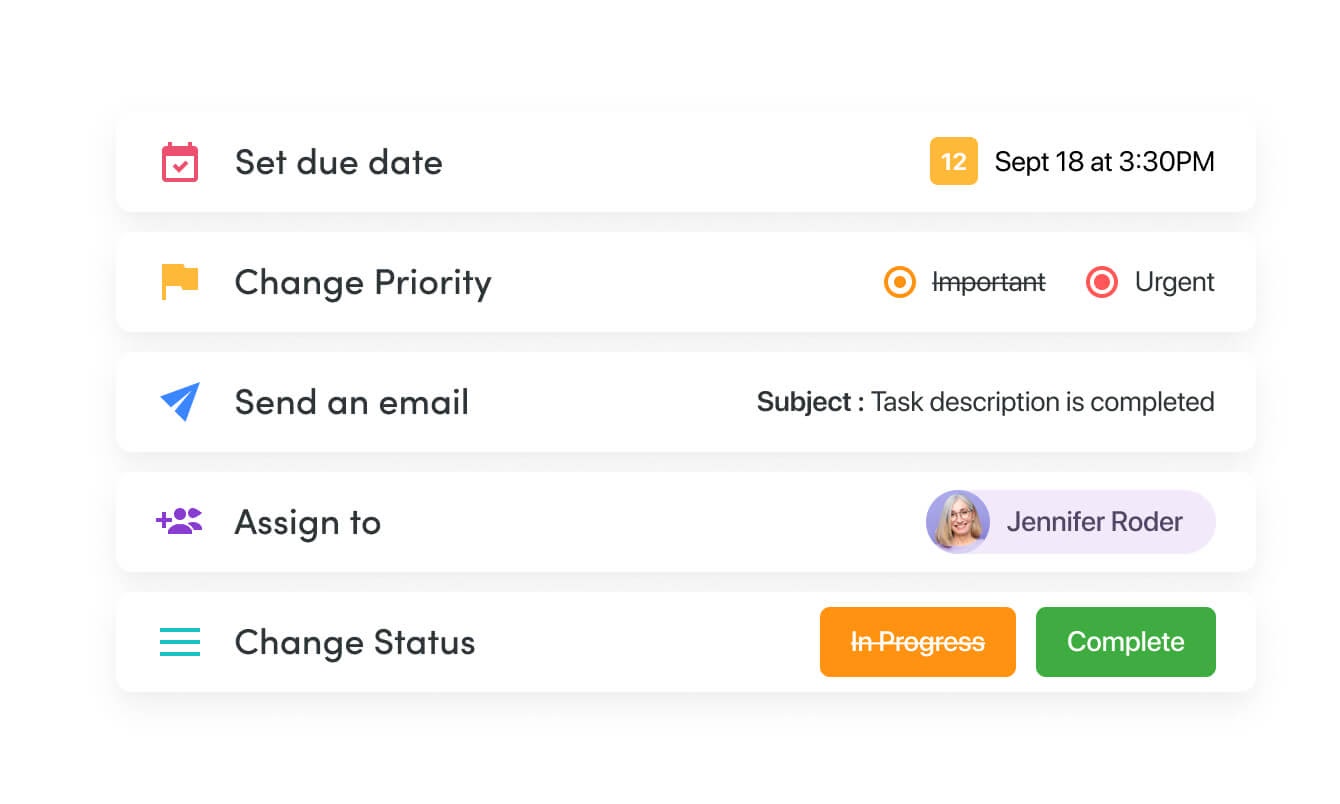
This way, you can focus on what truly matters to your company.
Powerful Reporting
To truly optimize a process, you need a way to measure progress. Software that provides powerful reporting capabilities will give you all the information you need to know about process performance. That way, you can identify where improvement efforts are needed and what changes you should make.
In SmartSuite, reports are designed with simplicity in mind. You can easily track performance and identify problem areas through the use of our reporting features.
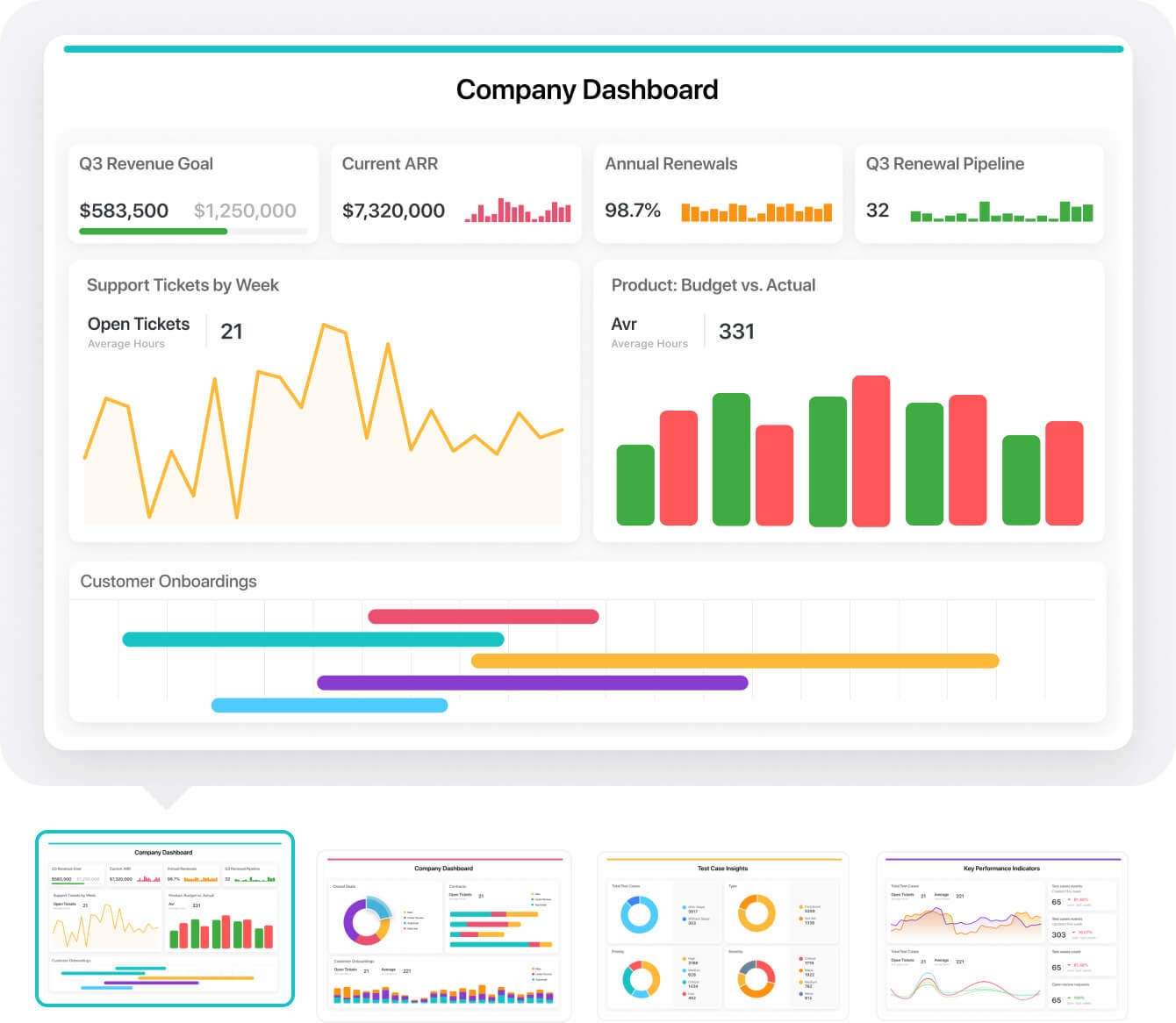
Reporting dashboards are fully customizable, too. This way, you can oversee the data that's most important to you. You also get access to multiple data view options to monitor your processes from different perspectives. For example, with our Gantt-like view, you can understand process dependencies and process phases to optimize process workflow.
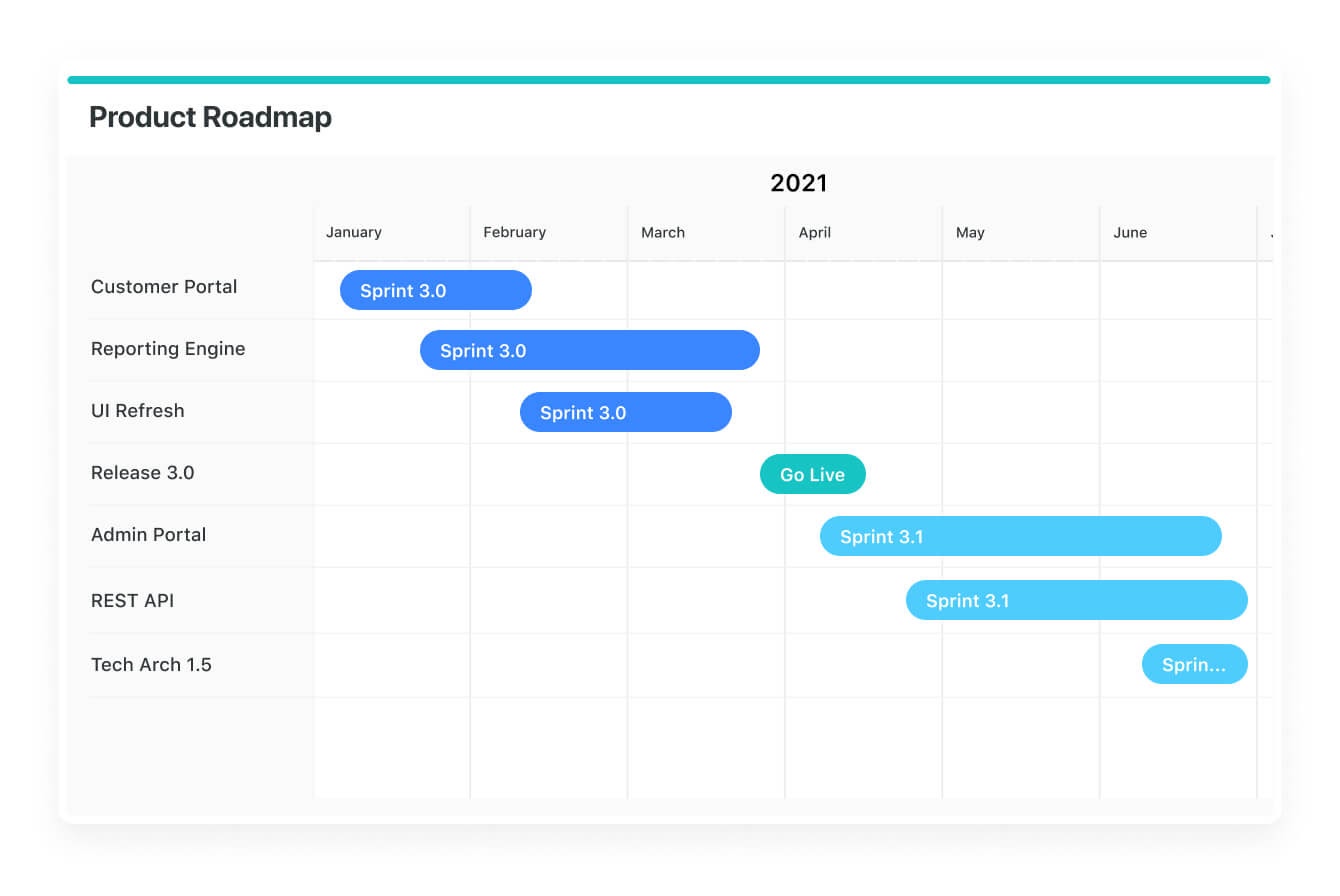
With the Timeline view, you can easily plan for process activities, milestones and tasks, and ultimately process execution.
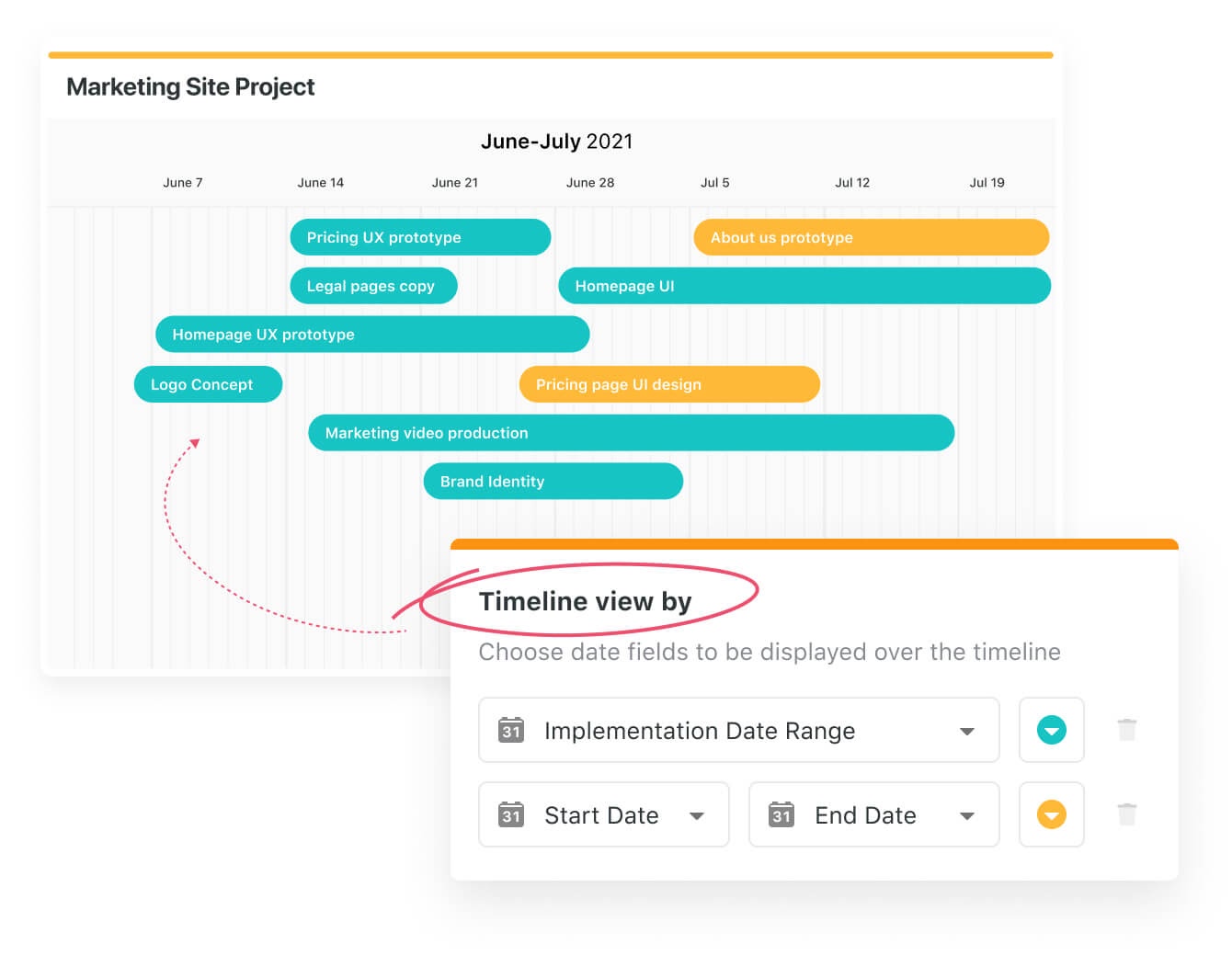
And the Kanban view gives you visibility and insight into process activities to help your organization make optimization decisions quickly.
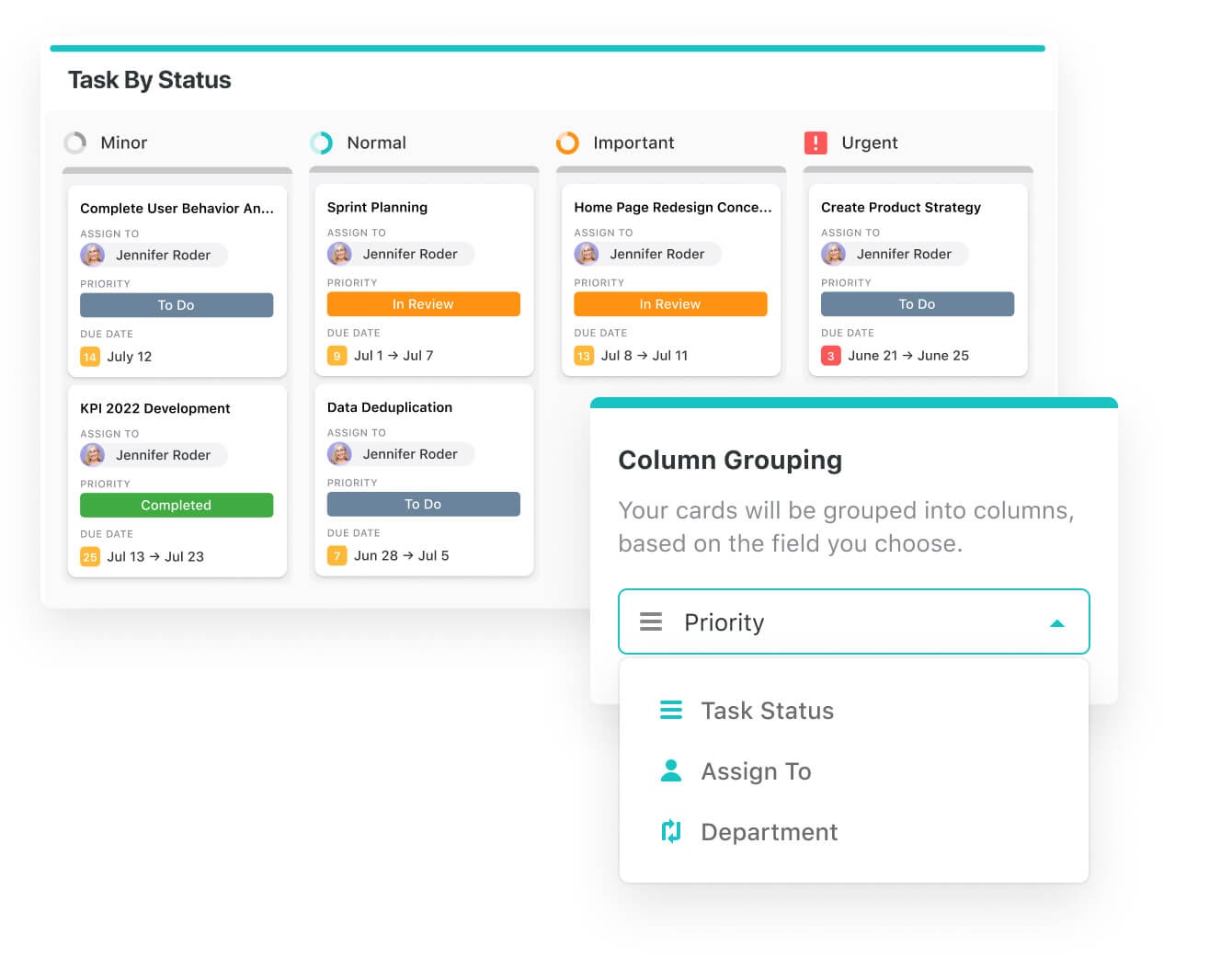
And, to be honest, that’s just the tip of the iceberg. To see a more thorough explanation of everything SmartSuite brings to the table, you can read our product overview page.
Let’s Optimize Your Processes
Now that you understand the basics of process optimization, the next step is to implement that information in your own business. The good news? You can start small. Identify a process where small changes can produce a big impact, and start there. Once you get familiar with the process, you can optimize more complex processes. Just make sure to use the right software during the process.
With SmartSuite, for example, you can map, edit, and optimize your processes in real-time. You can also invite team members and collaborate under one roof. This way, your entire time can benefit from process optimization. To start, we suggest you check out our project management template. It’s the best way to start on the right foot.